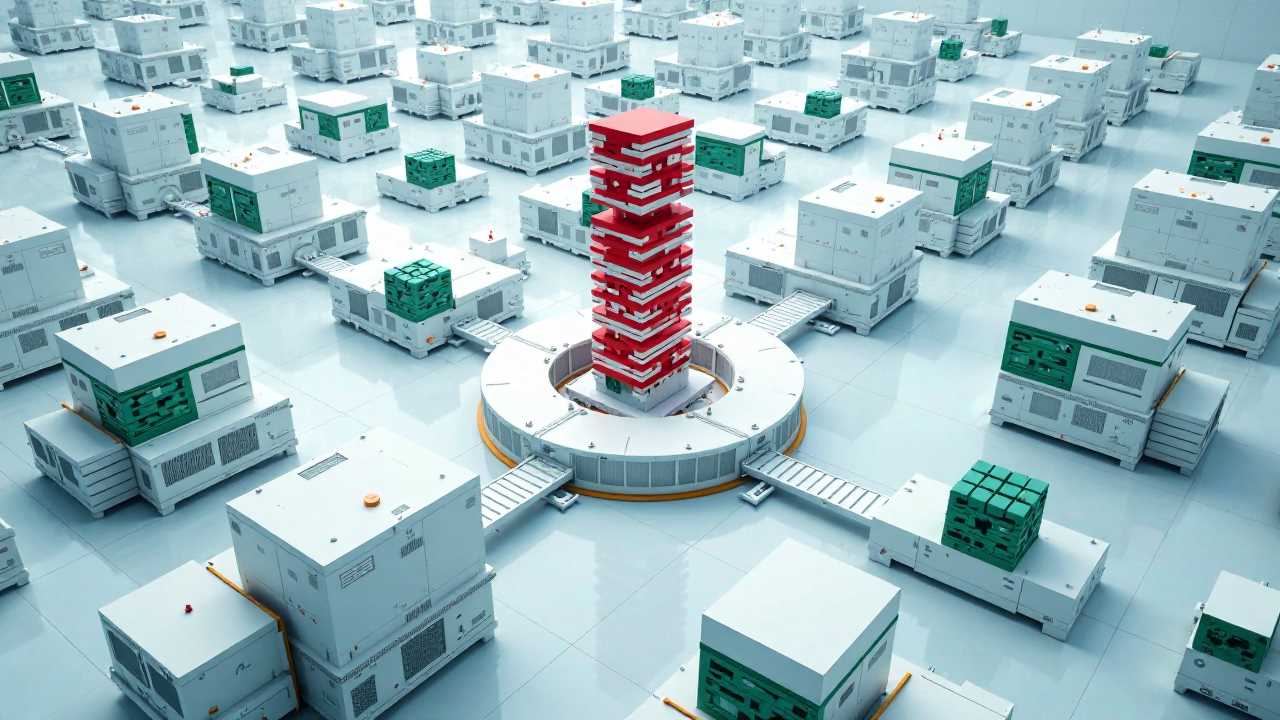
The Evolution of 3D Printing in Manufacturing Trends
In recent years, 3D printing has emerged as a transformative force in the manufacturing sector. This technology, also known as additive manufacturing, allows for the creation of complex structures layer by layer, offering unprecedented levels of customization and efficiency. As industries strive to meet the demands of a rapidly changing market, the integration of 3D printing into manufacturing processes is becoming increasingly prevalent.
The trends we observe today are not merely about technological advancements; they reflect a fundamental shift in how products are designed, produced, and delivered. By embracing digitalization, businesses can streamline operations, reduce waste, and enhance sustainability efforts.
Understanding Additive Manufacturing
Additive manufacturing is at the heart of the 3D printing revolution. Unlike traditional subtractive manufacturing methods, which involve cutting away material from a solid block, additive manufacturing builds objects from the ground up. This process allows for greater design freedom, enabling manufacturers to create intricate geometries that would be impossible with conventional techniques.
The implications of additive manufacturing are profound. It not only reduces material waste but also minimizes the energy required for production. As we move towards a more sustainable future, these benefits position additive manufacturing as a key player in the quest for greener manufacturing practices.
Customization: Meeting Unique Demands
One of the most significant advantages of 3D printing is its ability to facilitate customization. In a world where consumers increasingly seek personalized products, manufacturers can leverage 3D printing to meet these unique demands efficiently.
From bespoke medical implants to tailored consumer goods, the possibilities for customization are virtually limitless. This capability not only enhances customer satisfaction but also opens new revenue streams for businesses willing to innovate. By utilizing 3D printing, companies can produce small batches of customized products without incurring the high costs typically associated with traditional manufacturing methods.
Sustainability: A Greener Approach to Manufacturing
Sustainability is a pressing concern for industries worldwide, and 3D printing offers a pathway to more environmentally friendly practices. The traditional manufacturing process often results in significant waste, both in terms of materials and energy consumption. In contrast, additive manufacturing allows for precise material usage, significantly reducing waste.
Moreover, 3D printing enables the use of sustainable materials, such as biodegradable plastics and recycled metals. By adopting these materials, manufacturers can further lessen their environmental impact. As consumers become more environmentally conscious, businesses that prioritize sustainability through 3D printing will likely gain a competitive edge in the marketplace.
Automation and Efficiency in Manufacturing
The integration of automation in manufacturing processes is another trend that complements the rise of 3D printing. Automated systems can enhance the efficiency of additive manufacturing by streamlining production workflows and reducing human error.
With the ability to produce parts on demand, manufacturers can significantly cut down on inventory costs and lead times. This efficiency not only improves profitability but also allows companies to respond more rapidly to market changes. As the demand for rapid prototyping and short production runs increases, the combination of 3D printing and automation will become increasingly vital.
The Role of Digitalization in Modern Manufacturing
Digitalization is reshaping the landscape of manufacturing, and 3D printing is at the forefront of this transformation. By integrating digital technologies into the manufacturing process, companies can achieve greater transparency, traceability, and control over their operations.
Digital tools enable manufacturers to simulate production processes, optimize designs, and predict potential issues before they arise. This proactive approach minimizes downtime and enhances overall productivity. As industries continue to embrace digitalization, the synergy between 3D printing and advanced digital technologies will drive innovation and growth.
Challenges and Future Directions
While the benefits of 3D printing in manufacturing are clear, challenges remain. Issues such as material limitations, regulatory hurdles, and the need for skilled labor can impede widespread adoption. However, ongoing research and development are addressing these challenges, paving the way for more robust applications of 3D printing.
Looking ahead, we anticipate that advancements in materials science will expand the range of printable materials, making 3D printing even more versatile. Additionally, as industries increasingly recognize the value of sustainable practices, the demand for additive manufacturing solutions will likely grow.
Embracing the Future of Manufacturing
The impact of 3D printing on manufacturing trends is undeniable. By harnessing the power of additive manufacturing, customization, sustainability, automation, efficiency, and digitalization, businesses can position themselves for success in an ever-evolving marketplace. As we continue to explore the potential of 3D printing, it is clear that this technology will play a pivotal role in shaping the future of manufacturing. Embracing these trends will not only enhance operational capabilities but also contribute to a more sustainable and innovative industry.